Innovation and competitiveness
of boiler components
To be successful a business must constantly evolve and develop in response to the changing demands of its industry and customers. The continuous development of new products and services is the lifeblood of any business that is to stand the test of time.
Condevo® is no different, despite a 50 year record of success and, with a new name and a new portfolio of products, we are as committed as ever to the future of our industry.
We are therefore proud to present the first results of our hard work, carried out in the same spirit of collaboration and responsibility, which has always characterised our company.
Our new brand underpins the continuous development, motivation and dynamism of our management team. We are confident that the same values that have driven our growth over the first 50 years will inspire the new generation over the next half century.
Innovation and competitiveness
of boiler components
To be successful a business must constantly evolve and develop in response to the changing demands of its industry and customers. The continuous development of new products and services is the lifeblood of any business that is to stand the test of time.
Condevo® is no different, despite a 50 year record of success and, with a new name and a new portfolio of products, we are as committed as ever to the future of our industry.
We are therefore proud to present the first results of our hard work, carried out in the same spirit of collaboration and responsibility, which has always characterised our company.
Our new brand underpins the continuous development, motivation and dynamism of our management team. We are confident that the same values that have driven our growth over the first 50 years will inspire the new generation over the next half century.
Production of copper heat
exchangers for high-efficiency boilers
To obtain a high-quality product at ever more competitive prices, Condevo has completely automatized the copper exchanger production process in the last fifty years of activity.




Production of copper
heat exchangers for
high-efficiency boilers
To obtain a high-quality product at ever more competitive prices, Condevo has completely automatized the copper exchanger production process in the last fifty years of activity.

Production of "CondCell" set
heat exchangers for condensing boilers
The ‘CondCell’ set, produced in Italy, is based on a design that provides for a completely automated production process with over 50 robots.The stainless steel single coils are produced with pipes manufactured internally by automatic lines with “laser” welding.

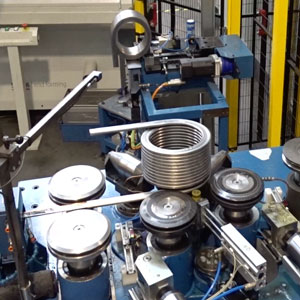

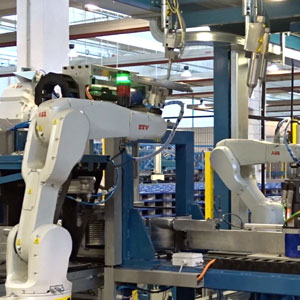
Production of
"CondCell" set
heat exchangers
for condensing boilers
The ‘CondCell’ set, produced in Italy, is based on a design that provides for a completely automated production process with over 50 robots.The stainless steel single coils are produced with pipes manufactured internally by automatic lines with “laser” welding.

R&D and Laboratory
The “CondCell” set is planned by our R&D Department in collaboration with our two Laboratories.

Condevo’s R&D Department is provided and uses the CFD simulations to reduce and optimize the time-to-market of the development (“virtual” products).
The new Laboratory Department, since 2014, is made up of two divisions:
1) Efficiency testing Laboratory : No 3 stations allow automatic testings and certifications, according to the most common and important standards (such as ErP) in three boilers with outputs from 1 up to 250 kW, either in central heating mode or water sanitary mode.
2) Life testing Laboratory: No 36 stations work in continous and totally automatic mode.
The monitoring and recording of each boiler’s operating data is managed by the automatic control system that can also be controlled, on request, by the customer directly (remote control).
The combined output of all Condevo testing stations amounts to over 2 megawatts.



R&D and Laboratory
The “CondCell” set is planned by our R&D Department in collaboration with our two Laboratories.

Condevo’s R&D Department is provided and uses the CFD simulations to reduce and optimize the time-to-market of the development (“virtual” products).
The new Laboratory Department, since 2014, is made up of two divisions:
1) Efficiency testing Laboratory : No 3 stations allow automatic testings and certifications, according to the most common and important standards (such as ErP) in three boilers with outputs from 1 up to 250 kW, either in central heating mode or water sanitary mode.
2) Life testing Laboratory: No 36 stations work in continous and totally automatic mode.
The monitoring and recording of each boiler’s operating data is managed by the automatic control system that can also be controlled, on request, by the customer directly (remote control).
The combined output of all Condevo testing stations amounts to over 2 megawatts.